Automotive Industry

Solutions for the Automotive OEMs, Tier 1, 2 & 3
Automotive manufacturing is a key field for Macrodyne.
With our extensive industry expertise, we have been supplying the world’s most notable companies in the whole automotive supply chain – OEMs, Tier 1, 2 & 3, in the manufacture of presses to a wide range of processes, new materials, and applications.
There are many challenges that automobile manufacturers face being in such a competitive industry. In addition to producing cars that meet the demands of consumers, cost and volume targets, and continuously evolving safety regulations, there are mounting pressures in creating lighter and stronger parts for improved fuel efficiency and abilities to withstand impact.
We understand those challenges and we help automotive manufacturers and suppliers to get to grips with innovative technologies and solutions to drive their products forward, exceeding expectations. Macrodyne Presses can be custom designed to attend to the unique requirement of each customer and fitted with electric control systems to ensure an optimal solution for automotive manufacturing applications. Considerations for repeatability and accuracy, as well as the ability to control tonnages and forming pressure, are essential for an efficient and successful production. Hydraulic presses offer versatility and can be used to produce a variety of parts by interchanging tools.
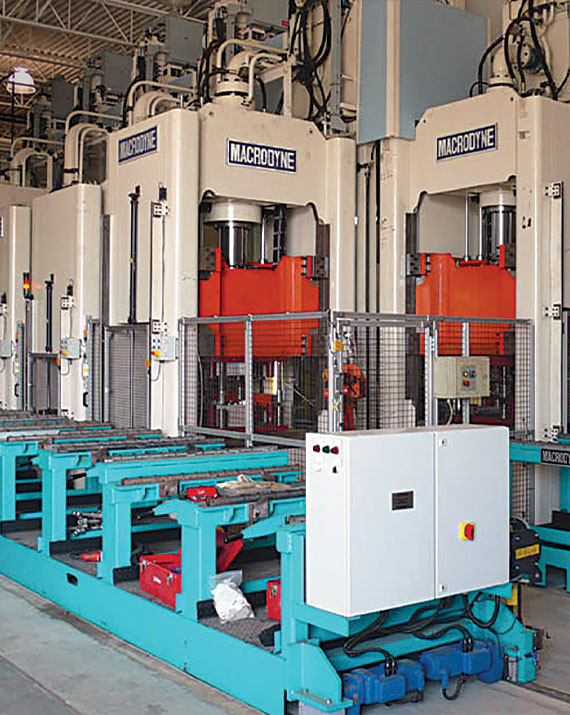
Hydraulic press line for automotive heat shields
Six (6) independent Macrodyne hydraulic, gib guided straight side presses are at the heart of this hydraulic press line which is used for the manufacture of automotive heat shields. line automation includes (3) servo coil feeders, (2) robots, servo transfer system, (6) scrap conveyors, die lubrication system, part vision system, and a powered quick die change system. This line produces a part every 6 seconds and a complete line changeover can be accomplished within 1 hour.
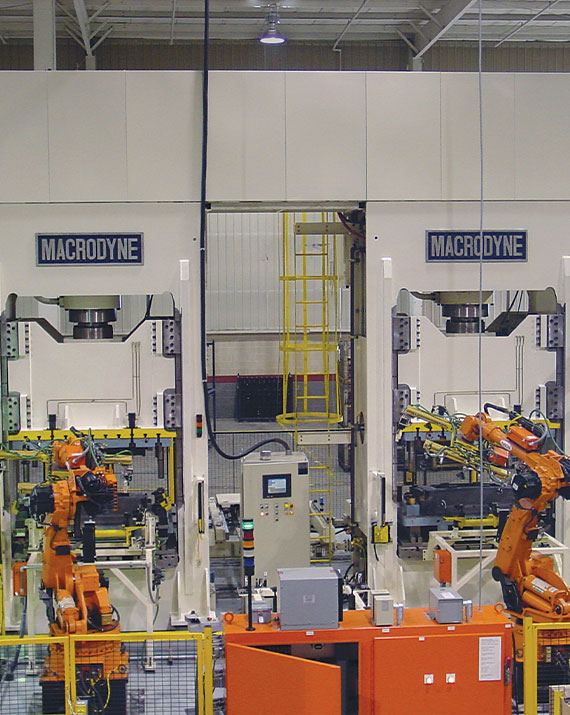
300 ton press cell for automotive sunroofs
This Macrodyne hydraulic press cell for the production of automotive sunroofs includes (2) Macrodyne 300 ton presses, (2) robots for part loading & unloading, and a Macrodyne die storage & retrieval system. Each press is equipped with a hydraulic blanking package, and automatic die clamping & lifting package. The Macrodyne die storage & retrieval system consists of (2) double die cart assemblies (each with dual push-pull devices, support & guiding rollers, and die plate latching assemblies), associated actuating devices, die plate assemblies, and rail systems.
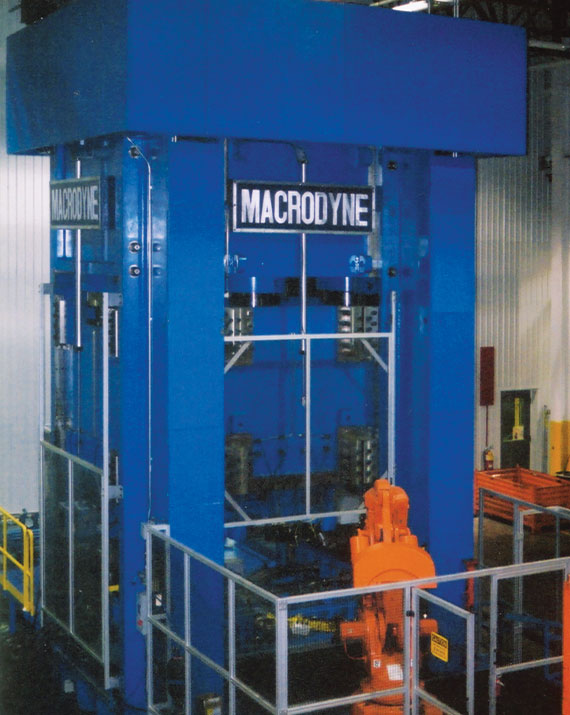
2500 ton tube hydroforming press
The above 2500 ton tube hydroforming press with 172″ x 84″ bed was designed for the manufacture of structure automotive components. The press was supplied with a heavy duty side slab style press frame designed to accommodate heavy eccentric loads, fixed positive stops to prevent over travel, and was integrated with a robot for loading/unloading.
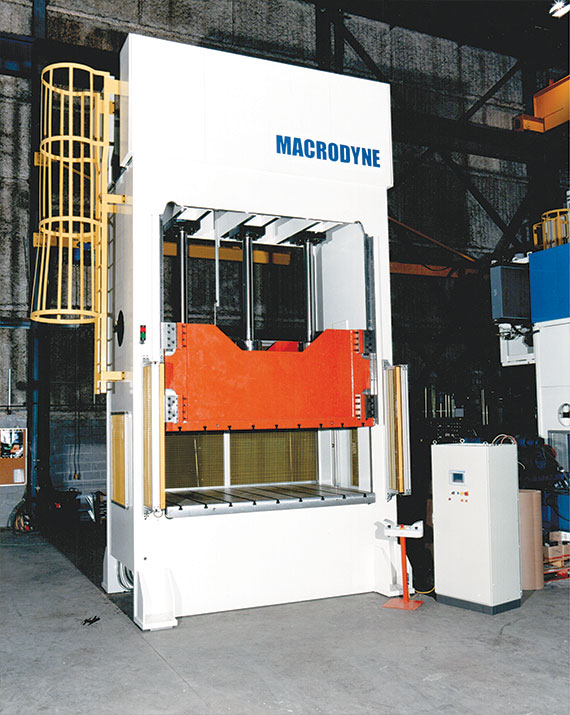
250 ton trim press
The above 250 ton trim press was designed for the trimming of automotive interior components, specifically dashboards for mini-vans. The press features a heavy duty monolithic press frame with operater access on all four sides, two single-acting main cylinders, and one double-acting pull-back cylinder. The press is equipped with a multi-pump based hydraulic drive package, auxiliary circuits for the trim tooling, safety package comprising lock pin arrangement with light curtains and safety fates, and a variety of process specific control features.
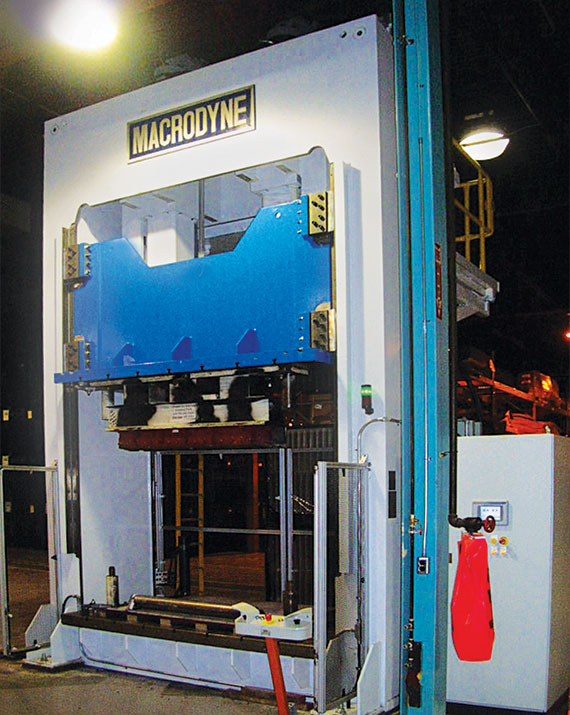
150 ton trim press
The above 150 ton press was specifically designed for a trimming application and is used to trim molded automotive wheel liners. The press features a thermally tress relieved monolithic style frame and deep, heavy, fabricated moving platen. The press is equipped with a multi-pump based hydraulic drive package, two double-acting main cylinders, three proportionally controlled auxiliary circuits for die functions, safety package comprising lock pin arrangement with light curtains and safety gates, and variety of process specific control features.
- Single and multi-point cushions
- Light curtain arrangements
- Laser scanners
- Fixed or sliding safety gates
- Work area LED lighting
- Remote diagnostics packages
- Blank holder and punch holder arrangements
- Automatic centralized Grease lubrication systems
- Single and multiple position slide locking arrangements
- Manual and automatic die clamping & lifting packages
- Data acquisition systems and many more
All presses can be optionally controlled by the industry’s most advanced systems that turn conventional presses into Servo-Hydraulic Presses. This state-of-the-art technology provides you with the steady, reliable force of Hydraulics, with advantages of Servo-controlled programmable motion, ultra-high precision, extremely fast approach/retract speeds, and energy saving.
Our President, Kevin Fernandes shared his insights on the auto manufacturing stamping trends to the Fabricating & Welding Magazine.